スーパーエンプラとは
金属と同等の強度や耐熱性を持ちながら、金属よりも軽量化、低コスト化を実現。
脱炭素社会の構築に向けて、世界中が注目している素材です。
スーパーエンプラとは「スーパーエンジニアリングプラスチック」の略称です。一般的な定義は、150℃以上の連続使用にも耐えられる耐熱性を持っていること、引張強度が49MPa以上であることと言われています(種類によってはさらに上の性能を発揮するものもあり)。その特性から金属材料の代替素材としても活用され、自動車部品、住設関連部品、バルブやポンプなど、さまざまな分野の基幹部品として使用されています。
ハジメ産業ではこれらの関連部品金属を中心に、今後さらに需要が見込まれる電子部品や医療分野にも挑戦していきたいと考えています。
- コストダウン
- 軽量化
- 後加工レス
- 防錆性
- 塗装レス
- オイルレス
- 絶縁性
- 意匠性
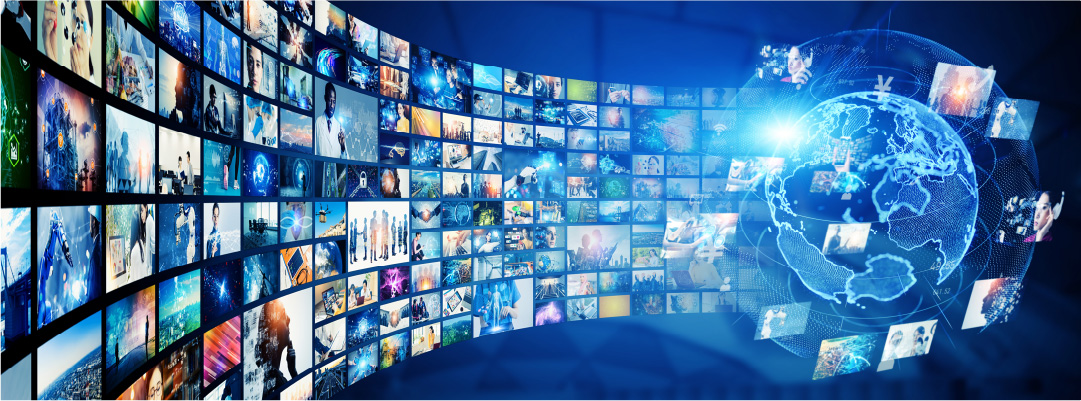
スーパーエンプラの歴史的背景
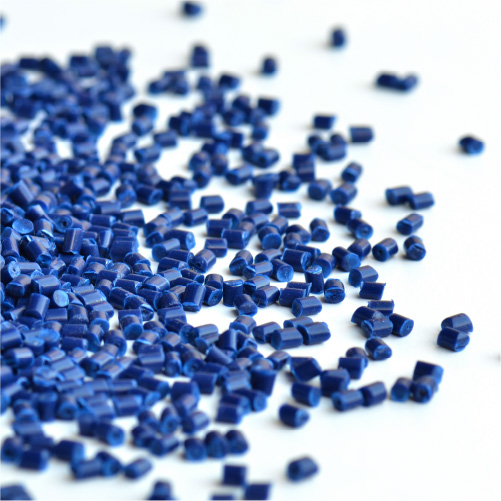
スーパーエンプラの歴史は1940年まで遡ります。始まりは1947年、米・デュポン社がフッ素樹脂の「PTFE(ポリテトラフルオロエチレン)」を販売し、その後、1966年に「PSU(ポリスルホン)」、1971年に「PPS(ポリフェニレンスルフィド)」、1972年に「PES(ポリエーテルサルフォン)」がリリース。日本では1973年に「PAR(ポリアリレート)」が開発されました。その後も続々とスーパーエンプラが開発され、世の中に広まっています。
プラ、エンプラ、
スーパーエンプラの違い
プラスチックは「熱可塑性樹脂」と「熱硬化性樹脂」に分けられます。熱可塑性樹脂は加熱することで加工できる樹脂。熱硬化性樹脂は加熱することで高分子化し、再溶融しなくなる樹脂を指します。熱可塑性樹脂で機能性を高めたものを「エンプラ」と呼び、それ以外は(汎用)プラスチックと分類されます。エンプラの中でも他の高分子材料と複合化したり、補強繊維などと複合化したものを「スーパーエンプラ」と呼び、エンプラを超える高強度と150℃以上の連続使用にも耐えるものを指します。
プラ、エンプラ、スーパーエンプラの分類(代表例)
分類 | 汎用プラスチック | 汎用エンプラ | スーパーエンプラ |
---|---|---|---|
種類 | PVC (ポリ塩化ビニル) HDPE (高密度ポリエチレン) LDPE (低密度ポリエチレン) PS (ポリスチレン) PP (ポリプロピレン) |
PA(ポリアミド) PC(ポリカーボネート) ポリエステル(PBT, PET) POM(ポリアセタール) 変性PPE(変性ポリフェニレンエーテル) |
PEEK(ポリエーテルエーテルケトン) PPS(ポリフェニレンサルファイド) PES(ポリエーテルサルフォン) PAI(ポリアミドイミド) PBI(ポリベンゾイミダゾール) |
耐熱性 | 〜100℃ | 〜150℃ | 〜250℃ |
コスト | 安価 | 汎用プラスチックより高価 | 汎用エンプラより高価 |
性能 | 低い | 高い | 極めて高い |
生産量(消費量) | 大量生産(全プラスチックの約8割) | 少ない | 少ない |
加工難易度 | 容易 | 汎用プラスチックより難しい | 極めて難しい |
スーパーエンプラの活躍フィールド
スーパーエンプラの用途は、工業製品が中心で自動車や住宅設備、バルブやポンプなどを中心に各種産業機器、食品機械、医療、容器、建材など、活躍のフィールドは広範囲にわたります。
暮らしの中で活躍する、金属代替素材「スーパーエンプラ」
分類 | 活躍フィールド |
---|---|
PEEK(ポリエーテルエーテルケトン) | インプラント、機構部品(軸受・ギア)、アルミニウム代替部品など |
PPS(ポリフェニレンサルファイド) | 自動車などの機構部品、バルブ、ポンプ部品など |
PES(ポリエーテルサルフォン) | 医療用中空糸膜、医療機器部品(内視鏡、透析器など)、食品機械部品など |
PAI(ポリアミドイミド) | 産業機器機構部品(軸受・ギア)、自動車(エンジン部品、トランスミッション部品)など |
PBI(ポリベンゾイミダゾール) | 自動車用軸受け部品、半導体・液晶製造装置の機構部品、シリコンウエハ関連部品など |
PPA(ポリフタルアミド) | 自動車(エンジン回り部品、電装部品)、センサー部品など |
PEI(ポリエーテルイミド) | 自動車(リフレクタ、フォグランプなど)、航空機部品、メガネフレーム、食品耐熱容器など |
PTFE(ポリテトラフルオロエチレン) | 調理器具、ガスケット、チューブ、テープ、表面コーティングなど(テフロンの商品名で有名) |
なぜハジメはPPSを採用したのか
PPSの良いところは高強度で耐熱性が高いことなどが挙げられますが、総合的に見て性能のバランスが良く、苦手な分野があまりない点です。そのため、自動車部品や住設部品、バルブやポンプ部品など、さまざまな用途でマルチに使えることが強み。現在、PPSの用途は6割ほどが自動車ですが、今後も軽量化による燃費向上などがテーマであり続ける以上、伸張していくはず。住設関連やバルブ、ポンプに使用される部品にも続々と採用されており、将来性が期待できます。
マルチに利用できる点においては、医療や半導体、航空機分野での可能性もあり、それぞれの領域でハジメ産業独自の成形技術などを駆使し、PPSの特性をうまく使いこなすことが可能性を広げるカギになると考えています。
PPSとは
1971年に市販された「PPS(ポリフェニレンスルフィド)」は、高強度、耐熱性、寸法安定性、難燃性など性能のバランスがよい材料として各分野で採用が広がっています。成形は難しいものの、形状の自由度が高いため、複雑な形状の電気部品や流動・温度の制御が必要な水回りの部品に使われることも。自動車部品分野では耐熱性、寸法安定性、耐薬品性から金属材料からの代替が進んでいます。

PPSの特徴
得られるメリット
- 耐加水分解性 160℃オートクレーブ(湿熱下)で90% 以上の強度保持率を示し、アラミドにはない優れた耐加水分解性を保有しています。
- 高強度 高い引張強度、剛性があります。耐衝撃性を高めるためにガラス繊維を混ぜ合わせ、強度を上げることもできます。
- 耐熱性 融解点は280~290℃で、高熱になりやすい部品にも使用可能です。低温環境への耐性も高く、約-20℃まで耐えられます。
- 耐薬品性 有機溶剤に触れても溶けない性質を持っています。酸やアルカリにも耐性があり、塗料を塗っても溶けることがありません。
- 難燃性 難燃剤を添加しなくても、自己消火性、低発煙性を発揮。燃えにくい性質を持っています。
- 食品衛生法適合 食品衛生法に適合している素材であるため、安全性が高く、食品や飲料水に触れる部品にも使用できます。
- 寸法安定性 成形後は吸水性が低いため、さまざまな環境下でも製品が型崩れをしない高い寸法安定性を持っています。
- 電気特性(絶縁性) 高温・高湿・高周波数のもとで、常に安定した電気的性質を示し、絶縁性があるのもPPSならでは。安全性の高い部品が作成可能です。
- 材料異方性 結晶性であるPPSは、繊維状強化剤や無機質フィラーを充填することで、より強度や性能が変化します。
- 比重 充分に結晶化した成形品のPPSの密度は1.38g/cm3程度。汎用プラスチックと違い、水に沈みます。
成形で生じるデメリット
- 寸法精度の不正確性 腐食性ガスの発生などから、金型内に溶融樹脂を安定的に充填するのが困難です。そのため、図面通りの寸法精度を出しにくくなります。
- 腐食性ガスの発生 成形時、高温により腐食性ガス(酸性ガス)が発生。このガスは金型や成形機を腐食させる恐れがあり、発生を最小限にする必要があります。
- 成形時のバリの発生 他の樹脂に比べ、成形時にバリが発生しやすい性質があります。成形形状の精度を向上させるためには成形後の正確なバリ取りが求められます。
PPSの世界的ニーズと将来性
スーパーエンプラの世界的ニーズは、2020 年新型コロナウイルス感染症の流行により落ち込みましたが、2022 年の販売量予測は約51 万t、2027 年予測は約65 万t と、EV化や車載電装化に伴う自動車分野での需要増加や、中国やインド・東南アジアなどの経済成長などを背景に大幅な市場拡大が予想されています。
スーパーエンプラ内でも特に注目の市場は「PPS」で、自動車の電動部品や電装部品、半導体装置部品やSMTコネクターなどの電気電子分野、水道混合水栓や給湯器の電磁弁など水回り部品でも活躍し、2022 年の販売量予測が約15万t、2027 年予測が約20 万t と、需要増加が見込まれています。
出典:富士経済「2023年 エンプラ市場の展望とグローバル戦略 上巻」
【スーパーエンプラ「PPS」の世界販売数量(予測を含む)】出典:2020年〜2027年予測…富士経済「2023年 エンプラ市場の展望とグローバル戦略 上巻」、2050年予測…弊社調べ
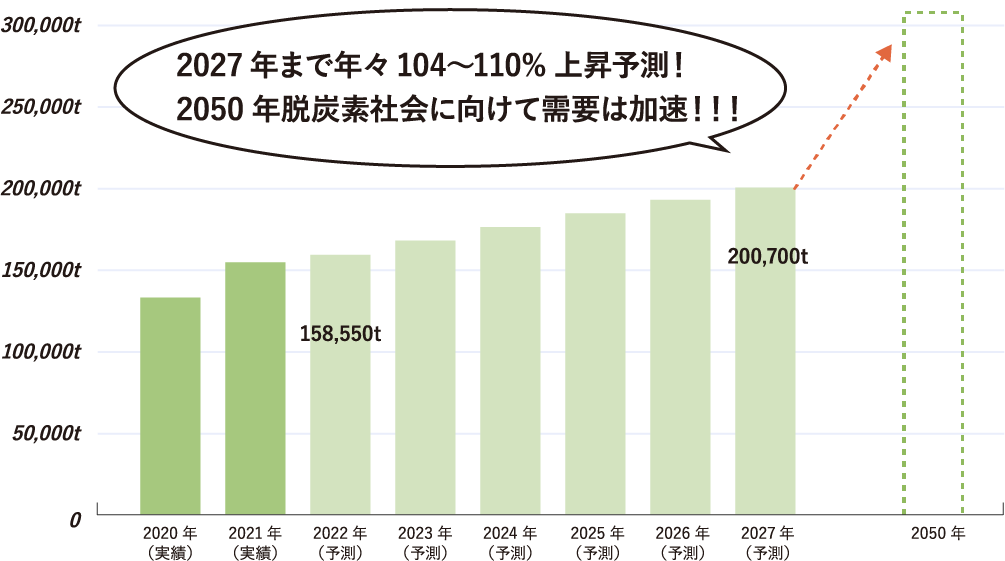
columnPPSとハジメの「未来予測」
ハジメ産業では「PPS」による成形・加工にいち早く取り組み、さまざまな分野でPPS 製品を開発、実績をつくってきました。2018 年度は、PPS 世界使用量12 万t のうち約3%(3,600t)を使用し、製品開発を実施してきました。いまなお、PPS 使用量は年々増加しています。 将来的には、これまで以上に新たな分野へ挑戦していくため、2050 年予測されるPPS 世界使用量30 万t のうちの5%以上(1 万t 以上)の使用量を目標にしています。また、PPS 単体の部品成形だけでなく、アッセンブリー 技術も取り入れることで、より完成度の高い製品づくりを目指していきます。
【ハジメ産業のお取引先業種売上と年間使用材料量の割合(国内)】(2021年度)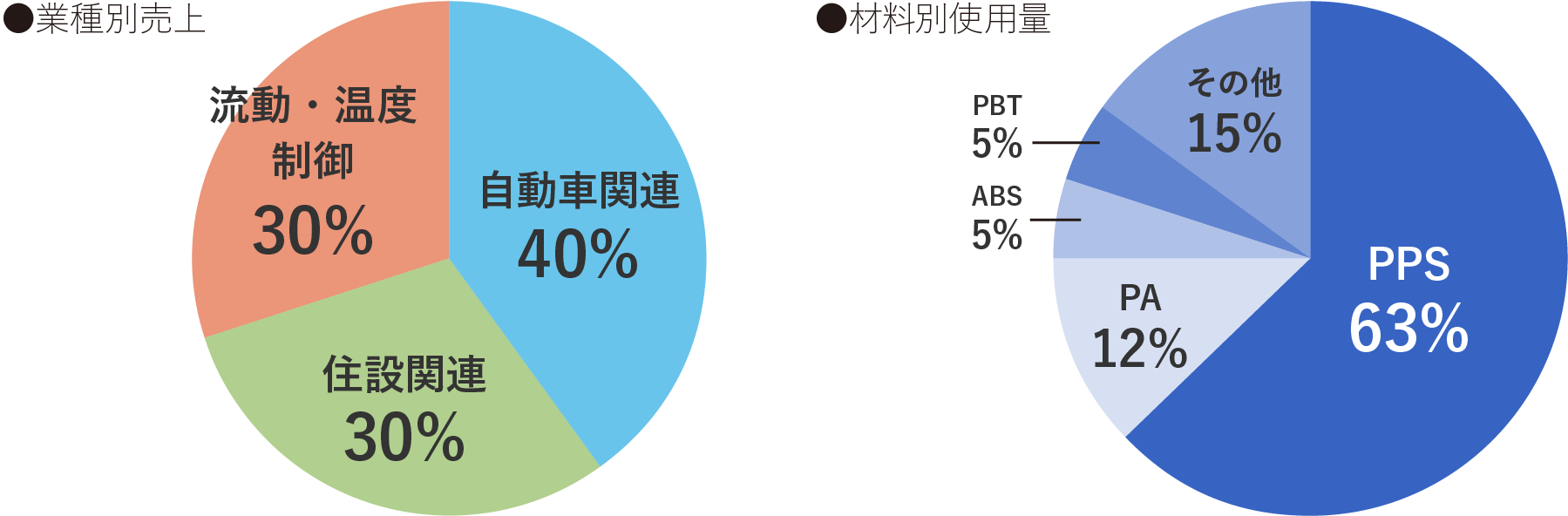